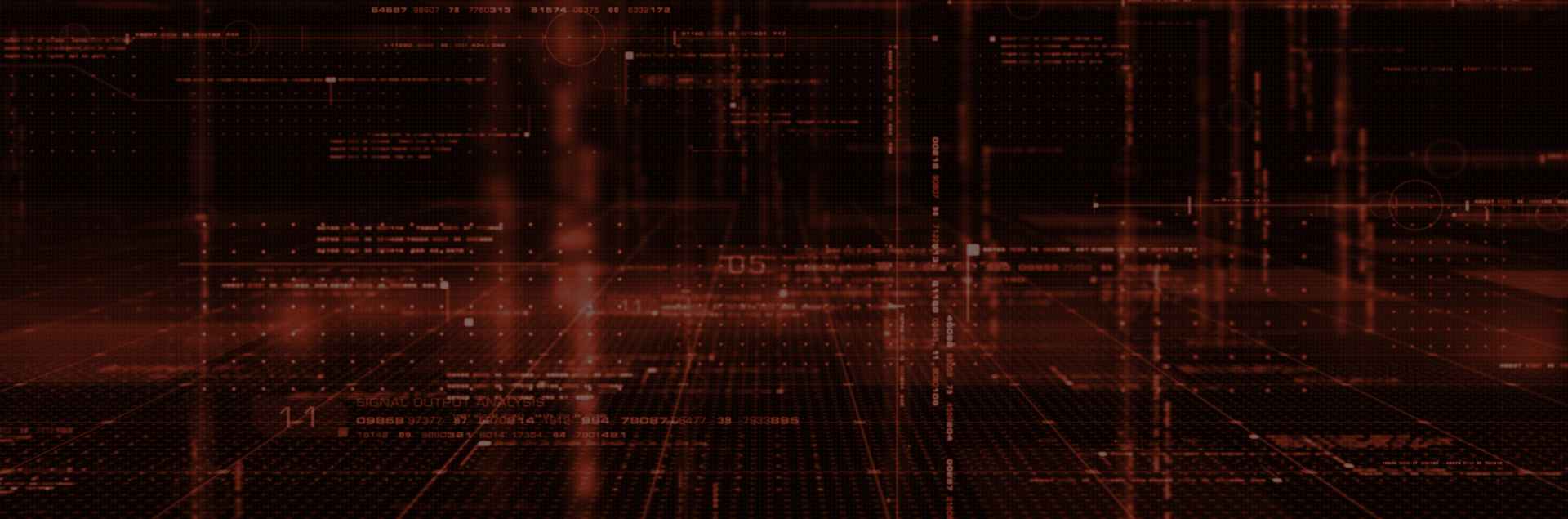
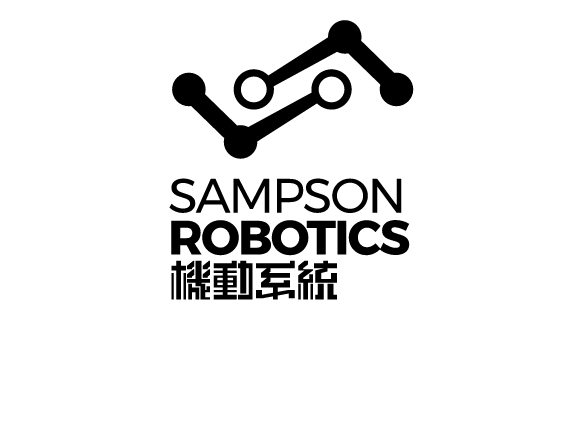

Streamlined System
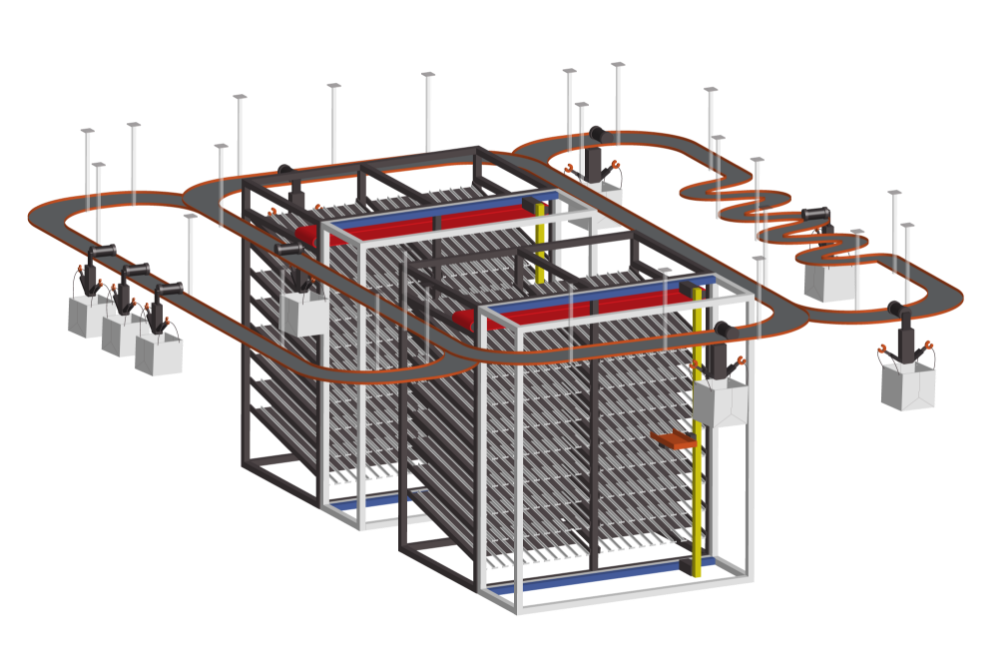

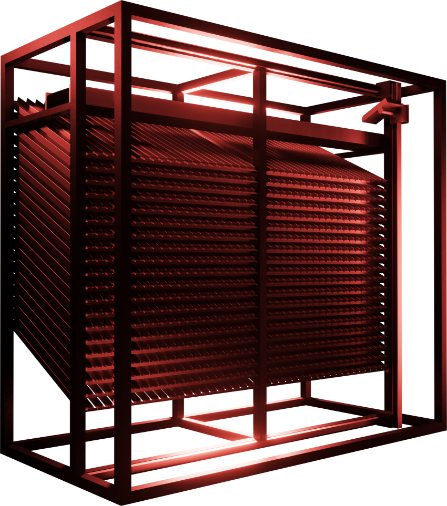
High Throughput
Offering a basic module as a product shelf with a footprint of 2.65 m2, it can accommodate a total of 5,320 items in the product shelf. Non-stop operation in picking items boosts to shorten the time used when comparing to the manual operation in the past.
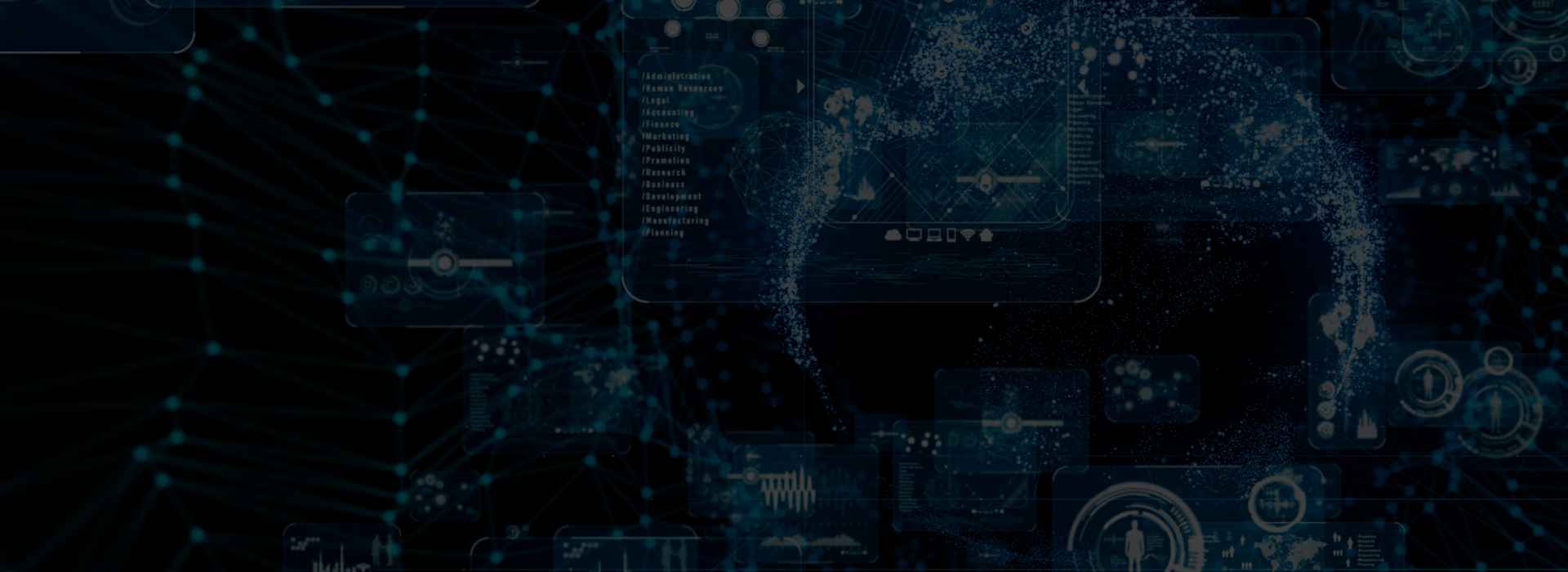
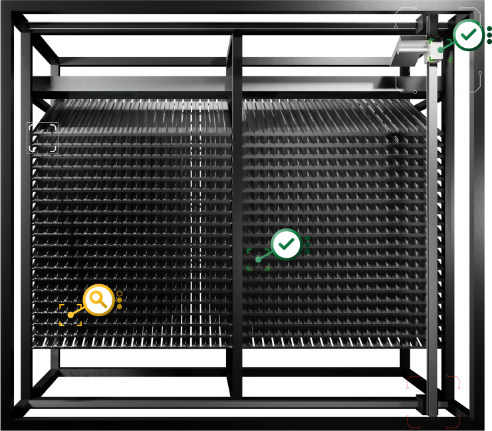
Seamlessly speaking, all components in the system carry their self diagnosis in checking their healthy status, such as low charge trolley will be moved and parked to the charging zone automatically when needed. Therefore, only some casual checkings are required such as dust/obstacle removal to the tracks.
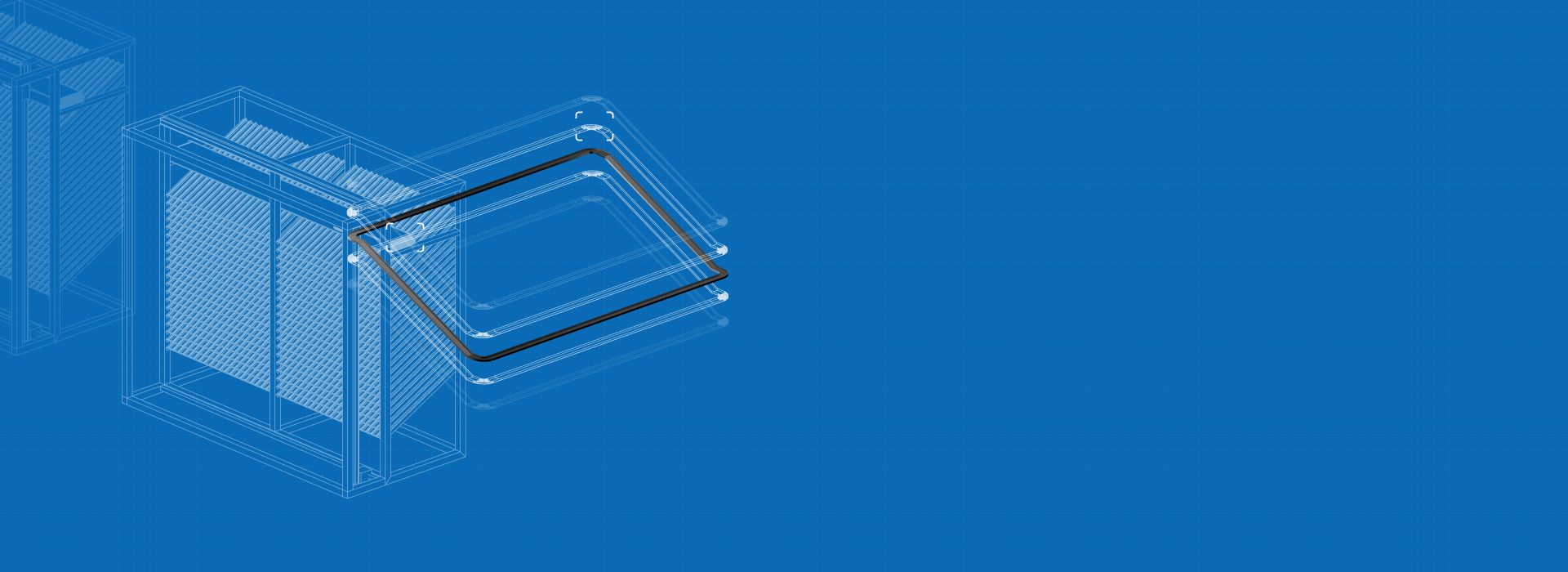
Customised rail design allows flexible routing around warehouse areas with the deployment of different numbers of shelves to maximize the use of precious warehouse space.
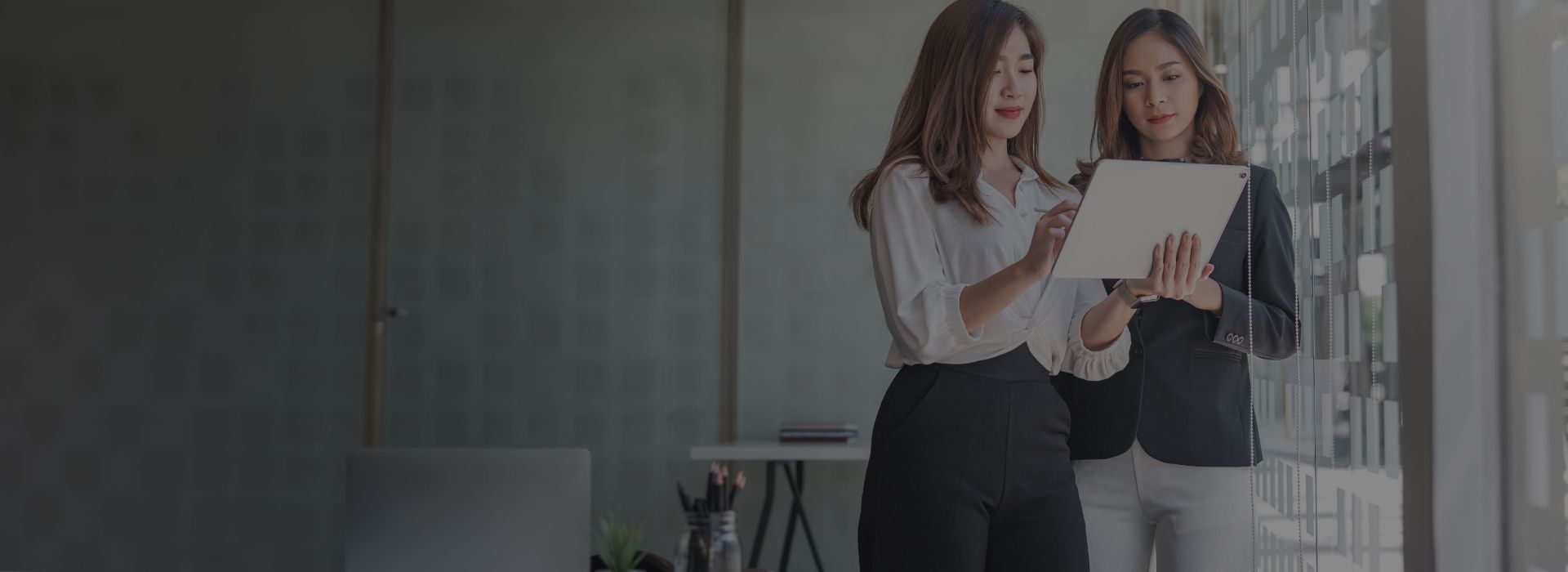
Items picking, receipt printing, order completing, goods refilling…all tedious and repetitive work can now be controlled at your fingertip in our operation APP (on a pad or mobile phone), easier and faster than ever. The system requires no technical skills on workers to operate a huge workload.
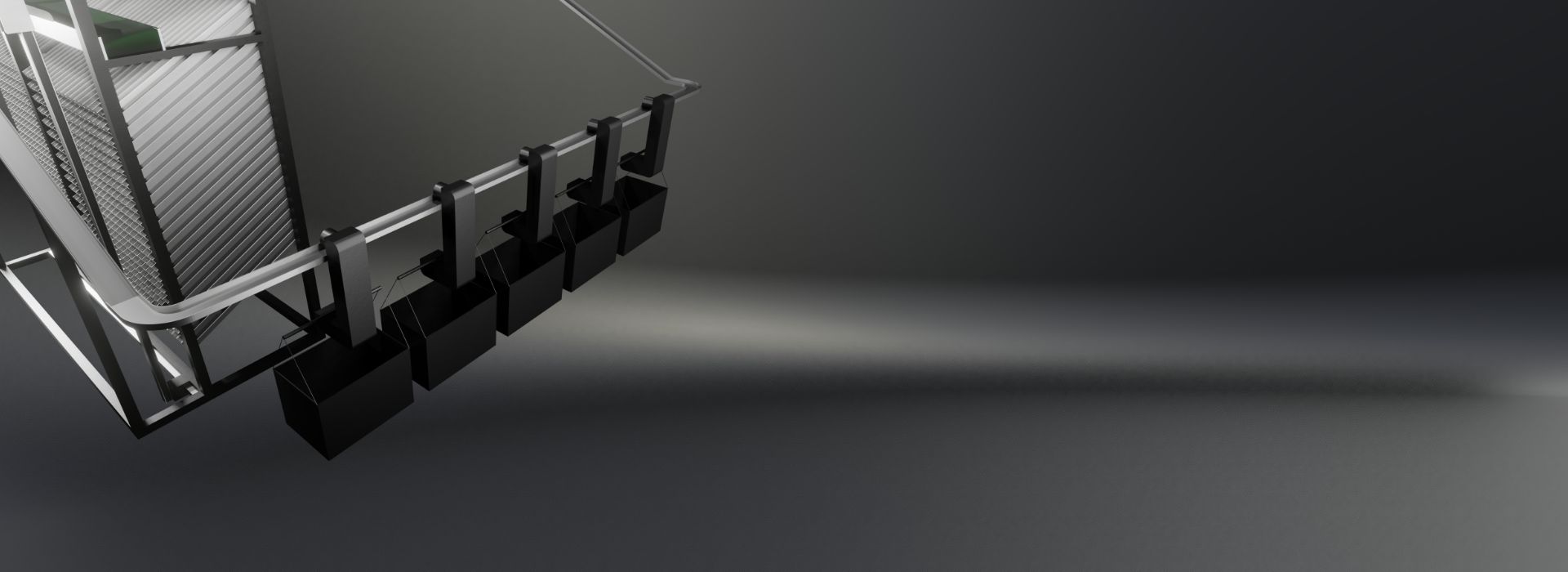
Programmed to pick up your orders before the peak hours even operators are not on shift. The deployment of more trolleys enables your fulfilment to meet the highest demand during the peak hours.
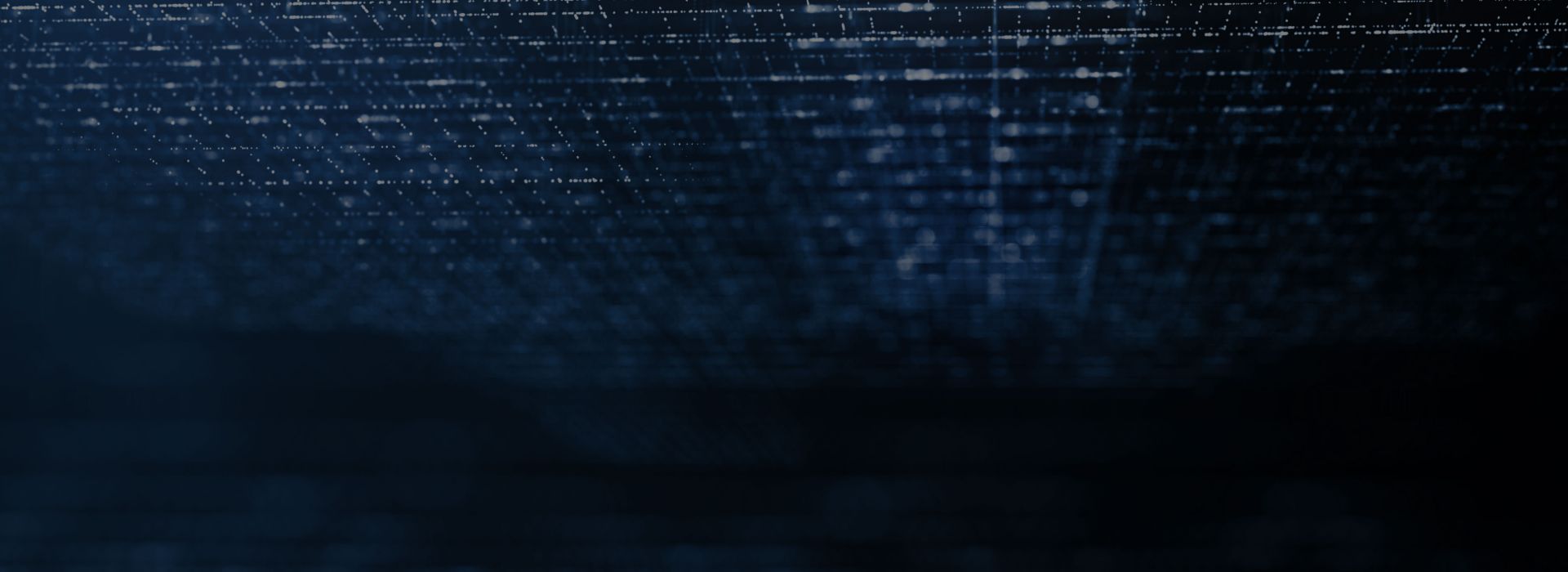
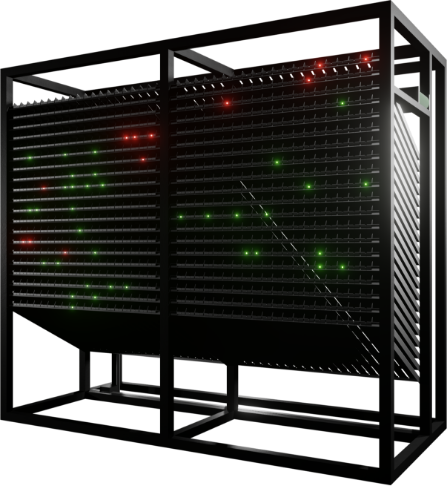
The system is like a vending machine. It will prompt operators to fill in low stock level items in non-peak hours to make sure maximum overall throughput. Due to system automation with barcode scanning in all processes, no skilled worker is needed to serve the system, minimizing your cost in human resources.
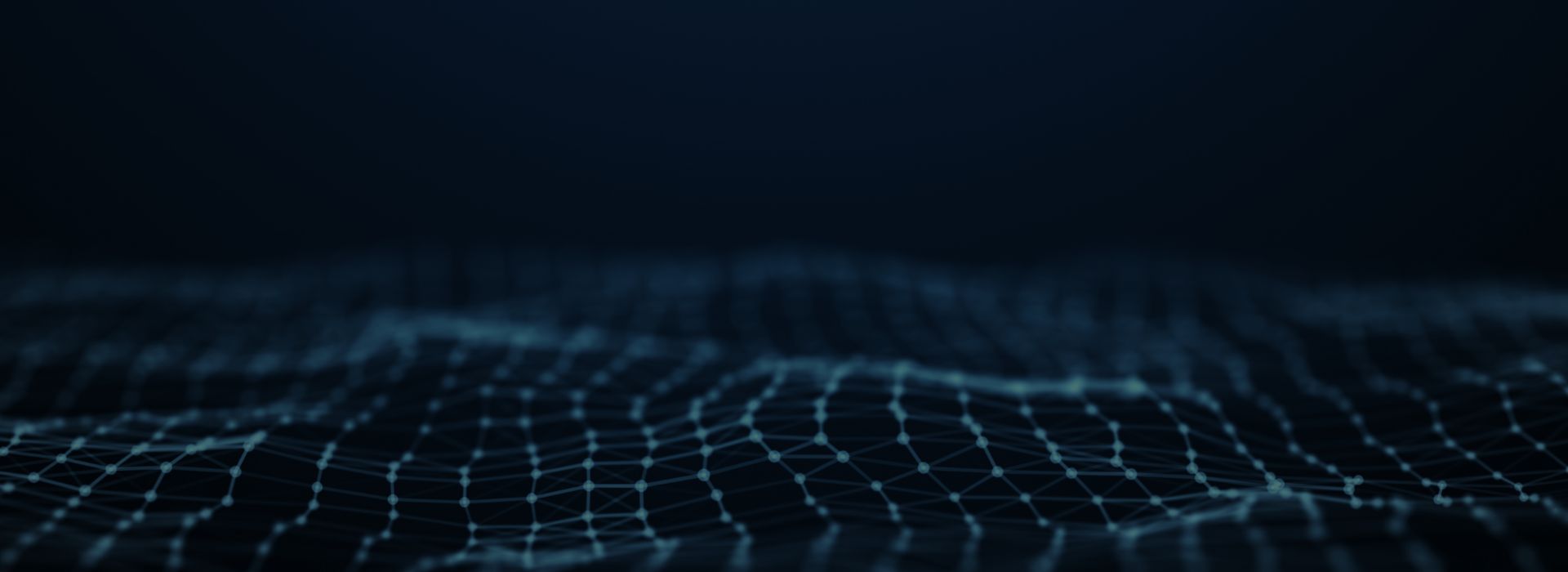
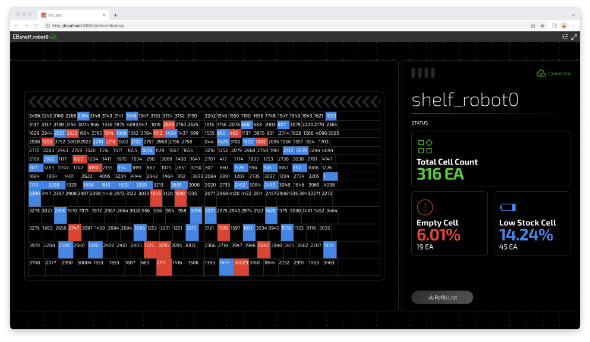
You can control remotely by the web-based console monitor to manage current jobs and health checking of the system in real-time.
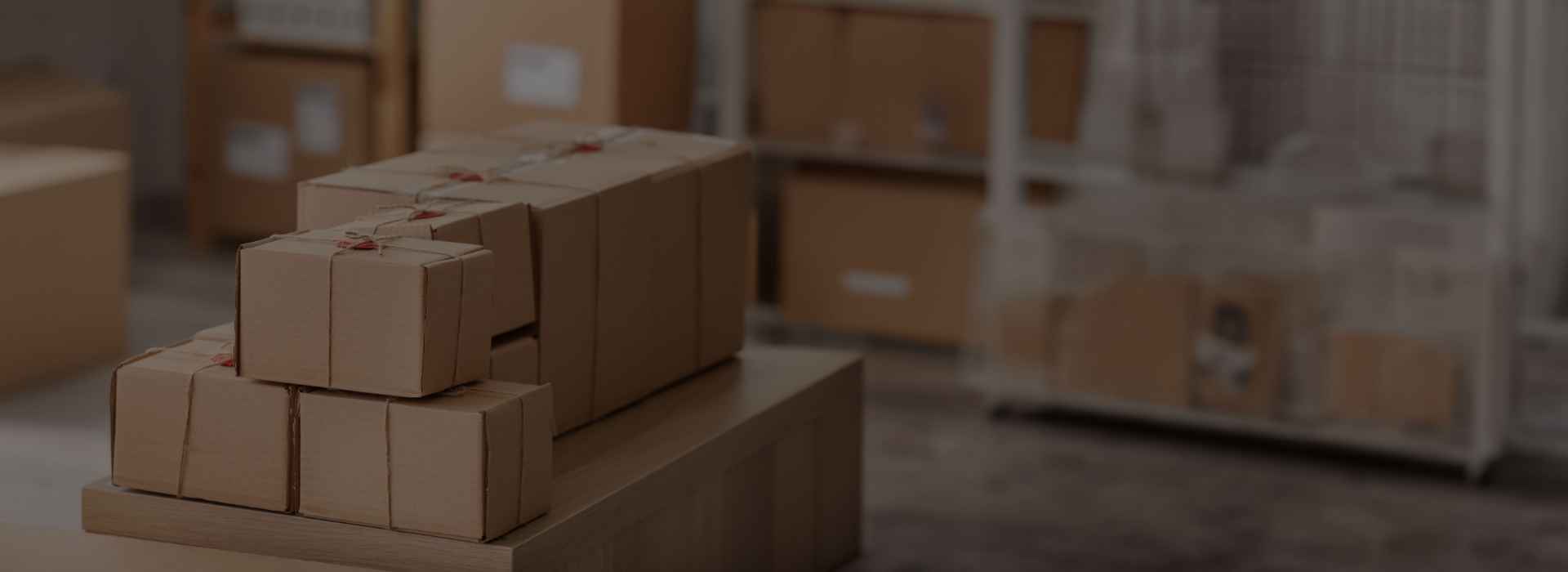
Facing with a problem of unattended orders after a long holiday, order fufillments are largely and precisely accomplished via robotic system, leaving greater flexibility in managing more workers to prepare the packaging within a shorter time before dispatch.
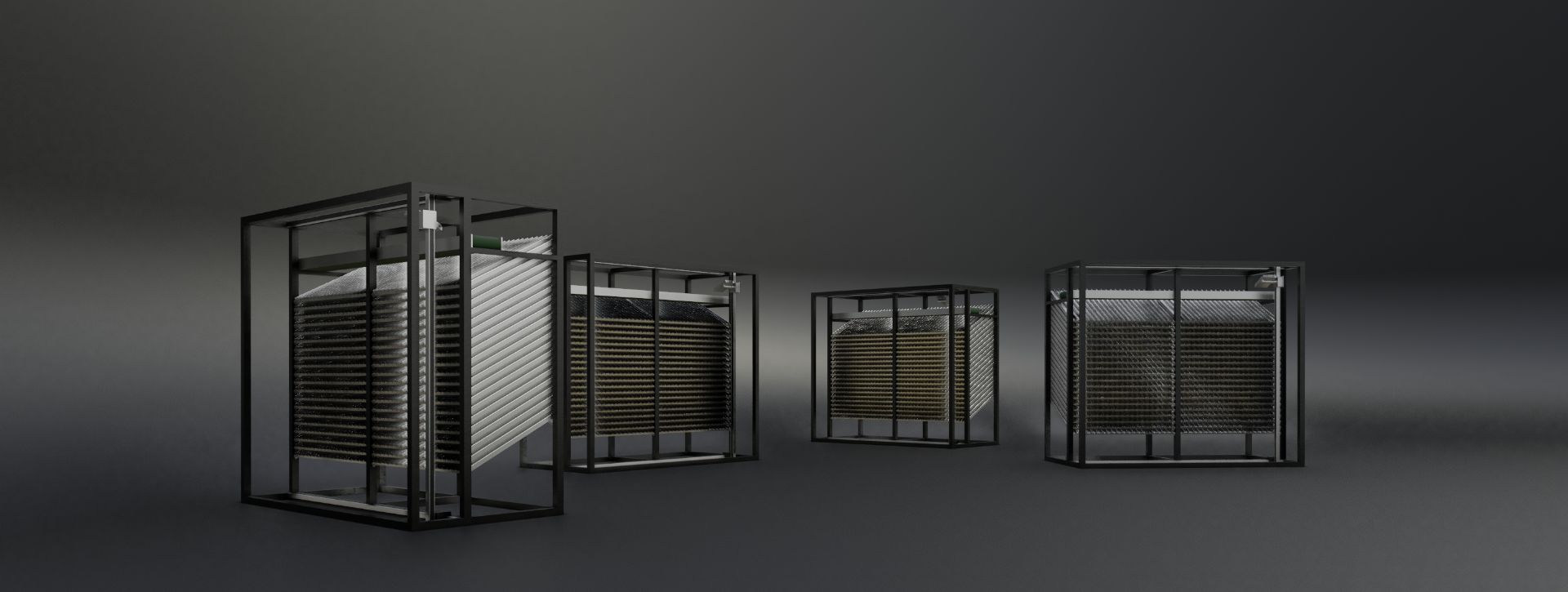
With its flexibility to be configured with multiple modules, it can comfortably fit in any warehouse environment by cascading the modules according to company scale, therefore, the system allows more items to be managed automatically.
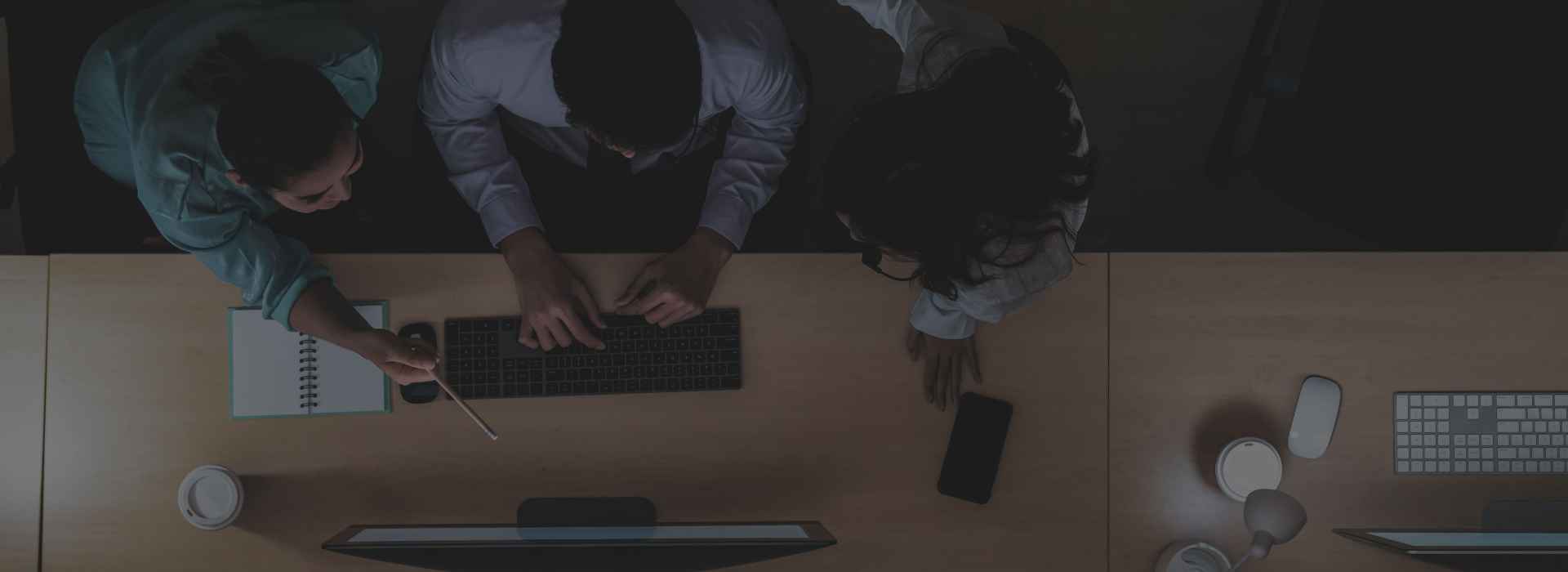
Startup with a single module via subscription, our service team will build up the system in a week and automation in picking up your items in your operation will then come in place.
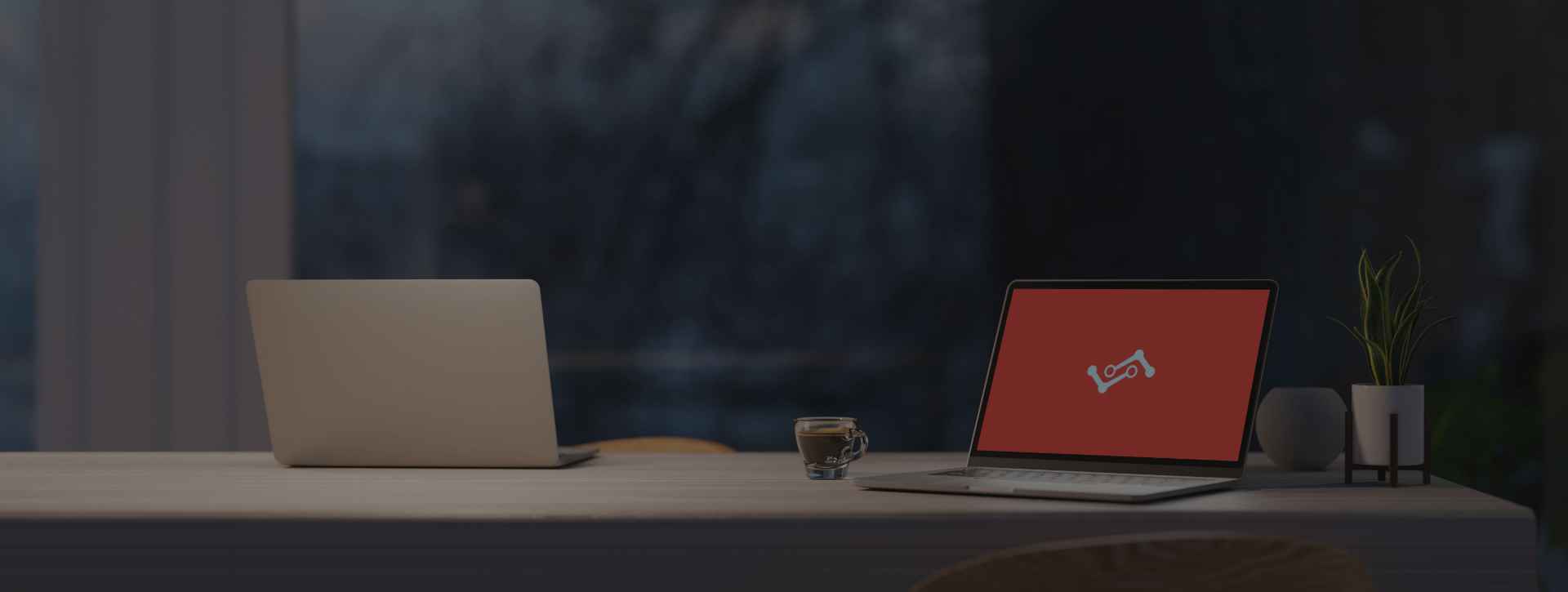
Smart console provides interface and standard operational procedures for your staff to prepare the packaging of the orders as well as a systematic approach to refill the items in the shelf in real-time.
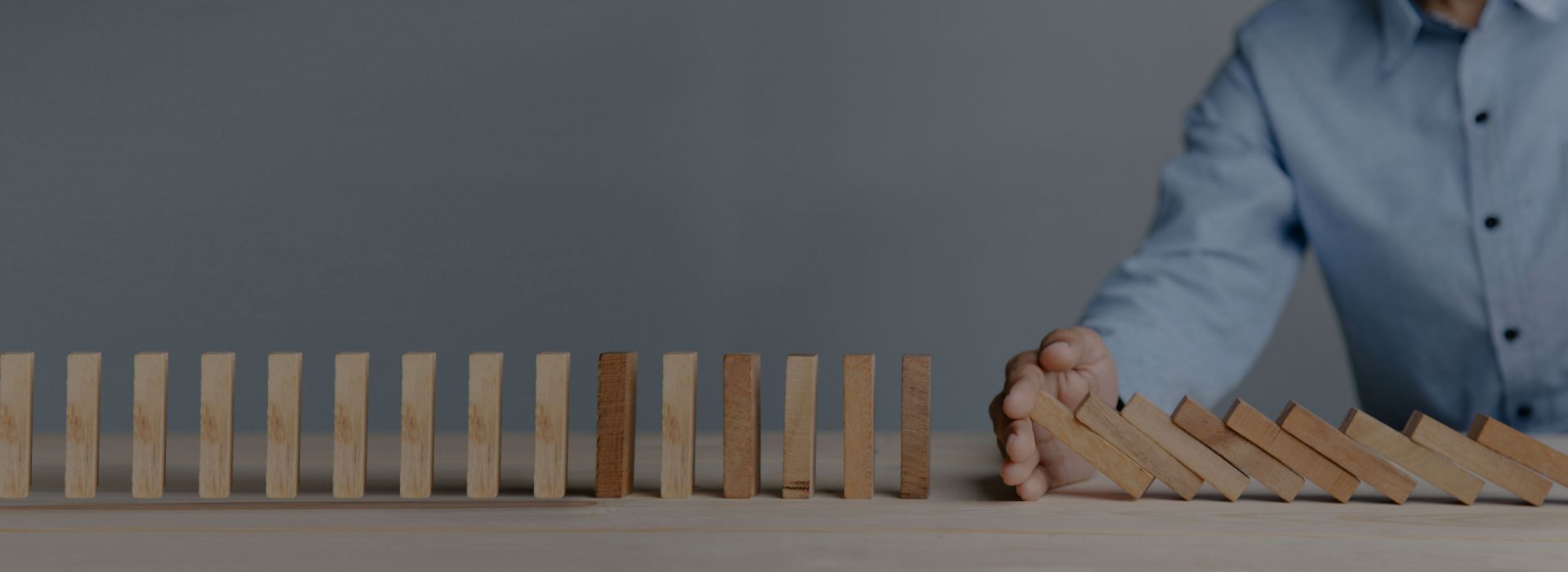
No more training to your workers to pick up the correct items as they are being selected automatically and collected to a trolley which stops in front of the workers to pack the items for an order.
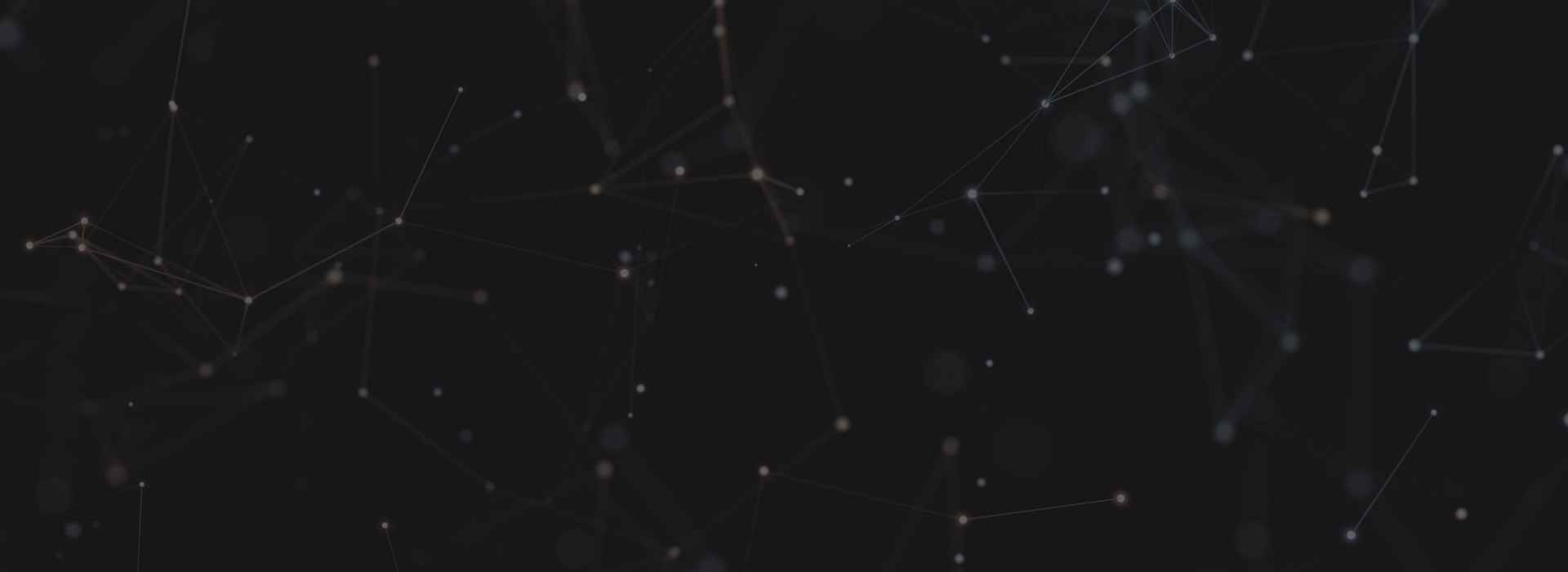
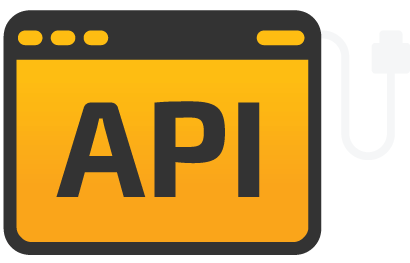
By using RESTful API, it provides simplicity, scalability, speed and ability to handle all data types from your system so that they can be integrated to our “SampsonRobotics” for taking care of.
Benefits
Greatest Importance
Optimum cost-benefit ratio is of the greatest importance – the shelf stores the fast moving items accounting for approximately 80% of the items being picked automatically on a daily basis.
Locations
Separated product shelf locations for greater efficiency
Integrate
Seamlessly integrate to the backend CMS system to facilitate an efficient deployment of full automation in the order fulfillment.
Flexible
Flexible investment plan to deploy the solution, for example, a subscription fee based on the per-item fulfillment basis.
Note
Specification of each shelf | 115 cm x 230 cm x 210 cm (Depth x Width x Height) |
---|---|
No of layers | 38 |
No. of Rails per layer | 14 |
No. of Items per Rail | 10 (Based on 10cm in length for a specific sample) |
Total no. of items (Max) | 5,320 |